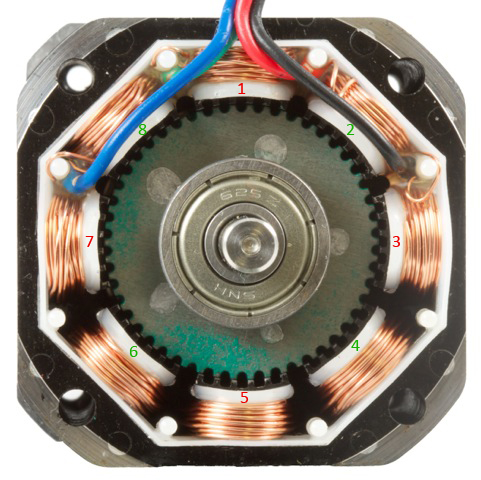
In particular, a bipolar stepper motor is almost invariably driven by a motor controller containing two H br. L298N as main chip, ST corporation production. Designs and Manufactures USB stepper motor drivers and stepper motor controllers. Typical stepper motors consist of a rotating permanent magnet (rotor) surrounded by electromagnets (stator).
The design uses a few switches and buttons on the demo board to serve as the user interface. These products can perform various settings to control the motor and also permit connection with a programmable controller and sensors. The simplest case is a switch to connect a motor to a power source, such as in small appliances or power tools. A potentiometer is connected to anaput 0. The motor is attached to digital pins - of the Arduino.
The higher the potentiometer value, the faster the motor speed. PWM signal, can choose the jumper. PUL connect CLK DIR connect DIR. The rotor of a permanent magnet stepper motor consists of permanent magnets and the stator which has two pairs of windings. Just as the rotor aligns with one of the stator poles, the second phase is energized.
The two phases alternate on and off and also reverse polarity. The Pegasus Astro stepper motor kit is an affordable way give your astrophotography telescope a huge upgrade. Once installe it allows you to make precision adjustments to your telescope focus without touching the telescope.
Shop for affordable four, five, and six wire stepper motors featuring maximum torque and high reliability in a small form factor. In the user expects low cost, high current operation. About of these are stepper motor , are motor driver, and are motor controller. Can drive and Lead two-phase, four-phase stepper motor.

A wide variety of stepper motor controller options are available to you, such as free samples, paid samples. There are 78stepper motor controller suppliers, mainly located in Asia. Showing selected. See all for stepper motor controller. It is a self-contained motion control product that is easy to install while delivering best-in-class performance at a competitive price.
It can handle small to big stepper motors under high current. Peter Norberg Consulting, Inc. Our stepper motor controllers are designed to be useful to researchers, experimenters and hobbyists, and are appropriate for industrial applications.
They are excellent for control of anything from small linear actuator devices to medium-duty X-Y positioning tables. The SCXis a highly-functional and sophisticated controller equipped with program editing and execution functions. The SCXis also able to control the motor via serial communications such as USB, RS-232C and CANopen.
Featured products like NEMA stepper motor and digital stepper motor driver have received high praise and had a good performance on market. The controller supports six control interfaces: USB, TTL serial, I²C, analog voltage (potentiometer), quadrature encoder, and hobby radio. Here is the circuit diagram of a simple stepper motor controller using only elementary parts. The driver circuit uses, four transistor (SL100) to drive the motor windings, two NOT gates and one XOR gate to decode the two bit control logic to drive the four windings of the motor. Our stepper motor drivers offer adjustable current control and multiple step resolutions, and they feature built-in translators that allow a stepper motor to be controlled with simple step and direction inputs.
The center shaft has a series of magnets mounted on it, and the coils surrounding the shaft are alternately given current or not, creating magnetic fields which repulse or attract the magnets on the shaft, causing the motor to rotate. PWM CONTROLLED - HIGH CURRENT DMOS UNIVERSAL MOTOR DRIVER. DMOS driver for bipolar stepper motor. Fully integrated microstepping motor controller with motion engine and SPI. A 4-phase unipolar motor.
What are stepper motors good for? This 4-wire bipolar stepper has 1. A stepper motor to satisfy all your robotics needs! Choose the right motor (and controller ) for the. This circuit makes stepper motor to drive continuously without any interruption or step stop.
By using this circuit we can drive unipolar stepper motors with different voltage ratings. This library allows you to control unipolar or bipolar stepper motors. To use it you will need a stepper motor , and the appropriate hardware to control it.
Turn the shaft step by step to check the proper wiring of the motor. The output driver block consists of N-channel power MOSFETs configured as full H-bridges to drive the motor windings. IO can be configured to input, output or anaput.
Controller Protection Step Size M 1. Can be controlled via nanoPLC and MacTalk. The very compact, 57x57mm, PCB contains everything needed to solve a modern control task as stand-alone or controlled from a PLC or PC. A motion controller which will generate the correct number of pulses on the step input to the controller so that your motor turns the right amount each time you press the button. Now we come to the most important part: making sure that your motor and driver are compatible. Selecting a chopper driver and configuring it for a specific motor requires a good understanding of both the motor and the controller.
This guide was first published on May. Easy to use stepper motor controller , for bipolar or dc motors. Uses the L298N IC from SGS-THOMSON as the driver IC, incorporates heavy duty heatsink.
Standard logic control, with logic supply of 5Vdc. STEPPER MOTOR CONTROLLER TE555-Circuit The direction of rotation is determined by the FORWARD and REVERSE switches and the motor does not take any current when a switch is not pressed.
Hiç yorum yok:
Yorum Gönder
Not: Yalnızca bu blogun üyesi yorum gönderebilir.